
LEARN MORE
LEARN MORE
LEARN MORE
LEARN MORE
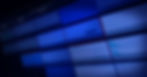
At SQUEAKS we provide manufacturing software
products and platforms for global manufacturing companies and industrial OEMs.
Our software products assist our customers in
achieving strategic business objectives for production efficiency, quality improvement, cost reduction, process control, along with team messaging and collaboration.
SQUEAKS gives you the power to personalizes the information your receive, making it easy to find the answers you want. With SQUEAKS, you receive only the information that is important to you!
Trust us with your communication platform like many other well-known companies have.
SQUEAKS is located in Louisville, Kentucky.
LEARN MORE
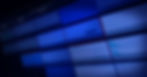
At SQUEAKS we provide manufacturing software
products and platforms for global manufacturing companies and industrial OEMs.
Our software products assist our customers in
achieving strategic business objectives for production efficiency, quality improvement, cost reduction, process control, along with team messaging and collaboration.
SQUEAKS gives you the power to personalizes the information your receive, making it easy to find the answers you want. With SQUEAKS, you receive only the information that is important to you!
Trust us with your communication platform like many other well-known companies have.
SQUEAKS is located in Louisville, Kentucky.
LEARN MORE
LEARN MORE
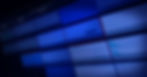
At SQUEAKS we provide manufacturing software
products and platforms for global manufacturing companies and industrial OEMs.
Our software products assist our customers in
achieving strategic business objectives for production efficiency, quality improvement, cost reduction, process control, along with team messaging and collaboration.
SQUEAKS gives you the power to personalizes the information your receive, making it easy to find the answers you want. With SQUEAKS, you receive only the information that is important to you!
Trust us with your communication platform like many other well-known companies have.
SQUEAKS is located in Louisville, Kentucky.
LEARN MORE
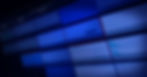
At SQUEAKS we provide manufacturing software
products and platforms for global manufacturing companies and industrial OEMs.
Our software products assist our customers in
achieving strategic business objectives for production efficiency, quality improvement, cost reduction, process control, along with team messaging and collaboration.
SQUEAKS gives you the power to personalizes the information your receive, making it easy to find the answers you want. With SQUEAKS, you receive only the information that is important to you!
Trust us with your communication platform like many other well-known companies have.
SQUEAKS is located in Louisville, Kentucky.
LEARN MORE
LEARN MORE
LEARN MORE
LEARN MORE
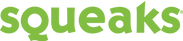
Escalating Alerts
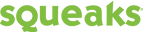
Some Alerts Cannot
Be Ignored.

At IGear, we have decades of experience in manufacturing. We understand the cost of downtime, we know how hard it is to find people, we know that means your team members need to cover more ground – and get more done with less.
We know everyone on your team comes to work every day wanting to do a good job and build a good product, but things (events) often get in the way.
These events, or what we call a Squeak, can include a piece of equipment dropping out of automatic, a key performance metric dropping below target, or someone at the line calling for help, to cite a few.
These events happen every day, every shift, every hour. When they happen, the logical question then becomes ... “Now what?”.

Drives Action
A Squeak can be automatically generated by a machine or database field, ...

SQUEAKS is founded on proven manufacturing principles including the
elimination of all waste in the pursuit of the most efficient methods and most productive workers.
We start by drawing attention to the concerning event. SQUEAKS provides
real-time, at-a-glance feedback – with a modern, digital twist – cutting response times from minutes to seconds.
Personalized
... or manually by a team member via an operator station, or the SQUEAKS app.

SQUEAKS is personalized. With SQUEAKS, you tune into what matters to you based on your responsibilities – minimizing distractions. SQUEAKS sends you only the information you need, when you need it, wherever you are.
Unlike traditional systems (stack lights, ANDON boards, HMIs, radios, etc.) that communicate limited amounts of information in more of a broadcast, noisy and open-loop manner; notifications from SQUEAKS are rich in content, targeted and closed-loop. SQUEAKS messages demand attention – they cannot be ignored.
Workflows

Workflows reduce the time to resolve a problem by providing guidance, work instructions, and supporting documents, etc. Workflow actions can be triggered and closed out manually by authorized personnel or automatically by the machine/controller itself – it’s up to you.
SQUEAKS seamlessly integrates with other applications. Events and associated Workflows can be initiated by other applications via SQUEAKS APIs and easily incorporated into a SQUEAKS message.
The SQUEAKS escalation process and rules provide a framework for ensuring that concerning events (downtime, product quality, operator calls, etc.) are addressed at the appropriate level of management based on their severity and complexity. An escalation process can also be initiated if a Squeak isn’t acted upon in a timely or correct manner.
Escalation Process

You decide how and when you want the escalated alert to move up the chain of command and how you want to be notified. In many organizations, the process includes a set of predefined escalation levels, each corresponding to a different level of management responsibility depending on the condition/event. For example, a Level 1 issue may be addressed by a team leader, while a Level 2 issue may be escalated to a department manager or area leader. More complex or critical issues may be escalated to higher levels of management, up to and including the executive leadership team.
The escalation process helps ensure that “issues or events” are addressed promptly and effectively and that the appropriate resources are allocated to resolve the issue. By escalating issues as needed, teams can quickly access the expertise and resources they need to identify the root cause of the problem and implement an effective correction action plan.





Extends Visibility

Following a concerning event, SQUEAKS focuses on what’s important now (WIN). Our goal is to help you and everyone around you achieve more and stress less.
More often than not, you are already capturing the concerning event in your PLC, HMI, or database. SQUEAKS taps into your existing system and unlocks the valuable information – communicating it to the right people wherever they are – and ensuring it is acted upon.
Unlike traditional plant communication systems that require you to be within line of sight of the stack light, HMI, or Andon Board; SQUEAKS extends visibility to mobile devices and smart watches. SQUEAKS runs on all your communication devices.
In addition to extending visibility, SQUEAKS provides greater insight by incorporating richer, more meaningful content. Whereas stacklights, HMIs
and Andon Boards often communicate in Morse code, SQUEAKS can attach
photos, videos, and documents that enhance communication and facilitate a
quicker resolution.
SQUEAKS drives accountability. From “Got It” to “Complete”, SQUEAKS
maintains a digital trail of every action taken throughout the problem-solving process – creating a greater sense of urgency while giving you the confidence that everything is covered.
After-the-fact, SQUEAKS provides reports that allow you to analyze what happened, how often, who was involved, and how long each step in the process took to complete. SQUEAKS enables an unprecedented level of countermeasures and continuous improvement leveraging factual information rather than guesswork.


Microsoft Teams Integration
Everything you can do with SQUEAKS can now be done from Microsoft Teams. If you are a manager and you use the Teams platform for communication, SQUEAKS can deliver real-time machine/process alerts and production reports directly to you in the Teams platform allowing managers and front-line workers to collaborate like never before.

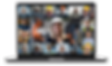